Multidisciplinary support at the design stage and during operation
Drawing from over 40 years’ experience in the nuclear industry, ENGIE Laborelec provides comprehensive services to prevent corrosion and other degradation phenomena in critical components, find workable solutions for obsolete or damaged components, and identify the root cause of failures to mitigate risk. We tailor our material-related services to the specific needs of nuclear power plant (NPP) operators. Complex and challenging missions are undertaken as a multidisciplinary effort involving Laborelec experts in materials, non-destructive testing, chemistry, vibrations, mechanics, and instrumentation & control.
Preventing failure or defects in metallic components
Laborelec provides comprehensive services to help nuclear operators fully understand ageing and avoid degradation in their installations. The safe operation of metallic components can be affected by ageing phenomena such as corrosion, fatigue, erosion, thermal ageing, and wear. We offer advice on how to address ageing at the design stage and during operation right up to full decommissioning.
Design-stage assistance involves advising on the materials to be chosen for every application. Based on decades of experience in the nuclear power industry, we rigorously examine the environmental parameters to which the material will be exposed throughout the component’s lifetime. This design-time assistance is backed up by our Materials Lab, where we work closely together with our chemistry experts to investigate and test material compatibility and assess the degradation risk.
We also co-develop and test pilot installations to investigate how the different components behave in harsh environments, including primary water, liquid metals, and molten salts, allowing the deployment of innovative new SMR designs to be de-risked.
Our operational support involves a wide range of operations, including non-destructive and destructive testing, advising on how to repair or replace components, and quality control inspections for coatings (NACE level 2 certified). We suggest customized inspection programmes based on the identified ageing mechanisms, allowing nuclear operators to optimize O&M costs. We also have experience handling and examining contaminated and irradiated parts in a hot lab.
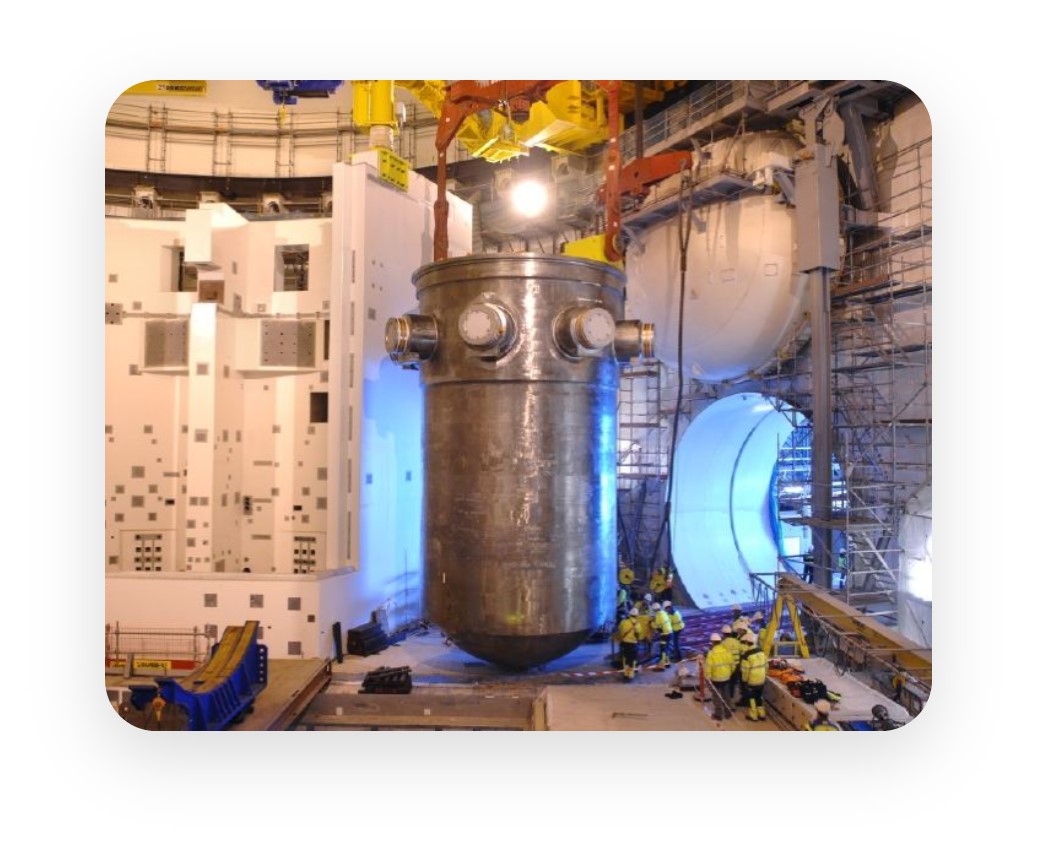
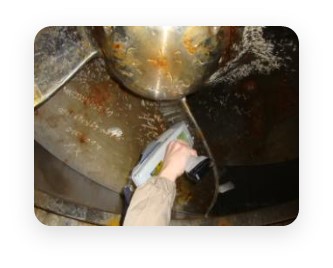
Preventing degradation in cables and other non-metallic components
Laborelec helps nuclear installation operators avoid degradation in non-metallic materials.
The materials used in cable insulation are a prime example of our work in this area. We offer a targeted service, assisting plants and network operators (through our cable management programme, for example) to identify which cables are at risk and need to be further examined or replaced.
The service includes on-site monitoring and measuring through inspections, electrical measurements, and using portable material analysis equipment. We can then recommend preventive and corrective maintenance based on our experience and in-depth knowledge of materials and equipment.
We offer similar inspection and maintenance services for non-metallic materials in other vital nuclear installation components, including seals, connectors, protection equipment, protective coatings (concrete and metallic substrates), and polymeric components in pumps and valves. The nuclear environment means that we pay special attention to radiation and radiological contamination as possible contributors to degradation.
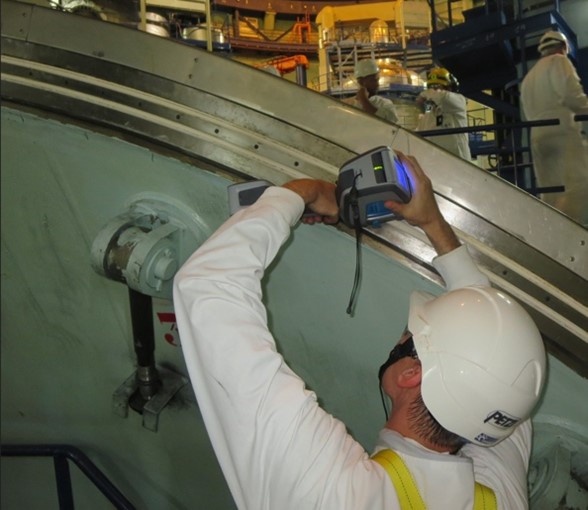
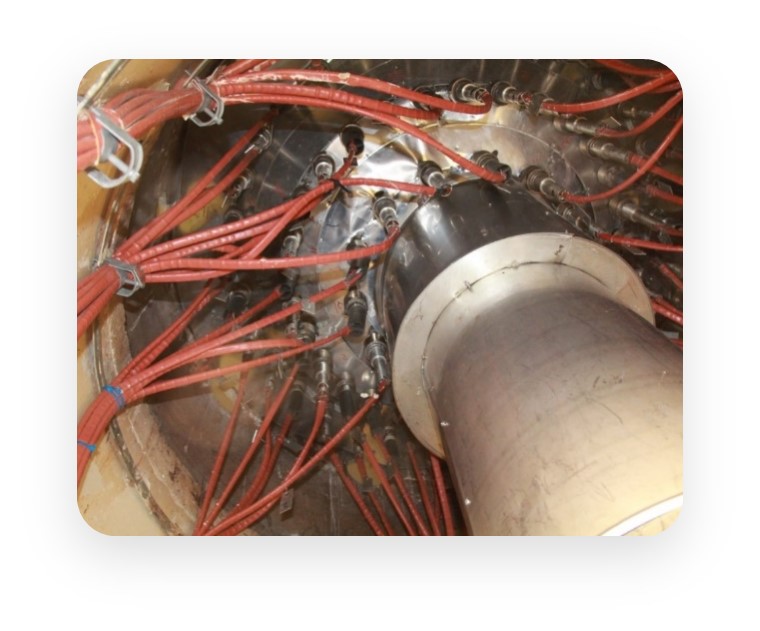
Workable solutions for component obsolescence
Laborelec helps NPP operators find workable solutions for any obsolescence that might occur during a plant’s lifetime. We carry out tests to evaluate the remaining lifetime of components and offer advice on how lifetime can be extended.
We conduct mechanical and functional tests on components as well as the materials from which they are made. The findings could allow us to compile a report to justify continued use, avoiding a more costly and time-consuming full qualification or re-qualification.
We also provide commercial grade dedication services, where we look for non-qualified off-the-shelf products on the market that could be viable or even identical substitutes for obsolete qualified components.
Retrofitting components through additive manufacturing
If critical nuclear installation components need to be retrofitted and no viable conventional manufacturing option is available, Laborelec can help with high-end metal additive manufacturing. We first analyze the component to see if additive manufacturing is technically and economically feasible. We might also propose to optimize the design before developing and optimizing the manufacturing process. We have already tested and qualified powders for nuclear applications.
After manufacturing the component, we carefully finish it off, including de-powdering and any other necessary thermal post-treatment or machining. We also carry out final quality checks to verify the component’s shape, dimensions, and mechanical properties.
With decades of experience in the nuclear industry and eight years’ operating an in-house additive manufacturing lab, Laborelec is the partner of choice for high-end component retrofitting.
Failure and root cause analysis
Laborelec’s Materials Lab plays a central role in our root cause analysis and failure remediation services. Whenever a failure occurs, we take immediate action to preserve, collect, and analyse relevant evidence of any kind, including as-found asset condition, operational circumstances, process parameters, and human interventions prior to and during the event.
The multidisciplinary investigation could involve carrying out laboratory procedures such as non-destructive testing, destructive material investigation, and chemical, mechanical, or electrical analysis. Then, we iteratively analyse dependencies and contingencies to determine all the factors contributing to the event and identify the root causes. Based on the findings, we produce a considered root cause analysis statement and advise on corrective and preventive measures.
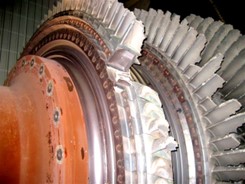
Scrutinizing material-related issues in a multidisciplinary approach
Here are some recent or current material-related assignments, illustrating how Laborelec provides both assistance at the design stage and ongoing support to address any issues that may arise.
Successfully addressing valve issues at Doel NPP
Leakage was observed some years ago in a primary water system at Doel NPP. It emerged that the leaks occurred only in valves of a particular design. Laborelec investigated the root cause in collaboration with the plant operator. We evaluated the risk that there was a general problem potentially affecting the hundreds of valves of the same type present in Belgian NPPs.
The leaking valves were inspected in our Doel hot lab, which is equipped to perform destructive and non-destructive tests on radioactive components. We also conducted an extensive NDT campaign to evaluate the status of the other operational valves of identical design. More than 1200 metallographic replicas were made, allowing us to identify intergranular stress corrosion cracks.
In-depth investigation led us to conclude that the cracking was due to an unfavourable microstructure resulting from a hardening treatment applied during the original manufacturing some 40 years ago. In close collaboration with the NPP operator, every valve exhibiting this unfavourable microstructure was identified and replaced.
Validating AM as a competitive solution for the nuclear industry
Laborelec plays a crucial role in the EU-funded NUCOBAM project which was launched in 2020 and will conclude in 2024. An acronym for NUclear COmponents Based on Additive Manufacturing, NUCOBAM was set up to validate metal additive manufacturing as a safe and competitive solution in response to component obsolescence in the nuclear industry.
Laborelec is fully engaged in high-end additive manufacturing in metal, deploying its expertise and highly regarded Linkebeek AM Lab to produce critical components such as valves and filters, and subjecting them to non-destructive tests.
In September 2023, Laborelec hosted the NUCOBAM Fab Lab event and workshop, inviting actors working in the nuclear research environment and industry as well as safety regulators to share their experiences, coding routes, and expectations in additive manufacturing. As part of the Lab tour, we presented the techniques and outcomes developed in NUCOBAM.
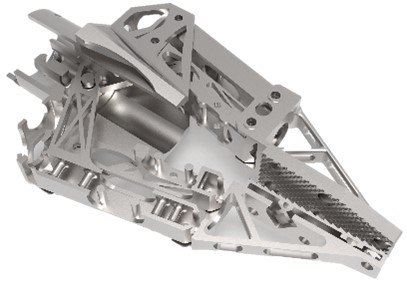