Laborelec is investigating a technique to chemically clean boiler tubes in a heat recovery steam generator while still in operation instead of during an outage. The results of lab tests are promising.
December 2023
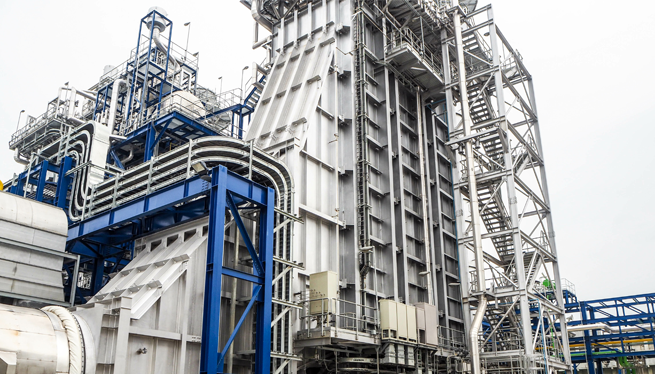
A known cause of failure and damage occurring in combined cycle plants is the fact that corrosive products are transported to the high-pressure evaporator, leading to oxide deposits in the boiler tubes. The traditional approach is to remove these layers during an outage, but this is a costly procedure with a significant environmental impact and some risk to boiler integrity. In addition, flexible operation increases the risk of abnormally thick, porous oxide layers being developed, which can lead to tube failure and unplanned shutdowns.
An alternative solution would be to inject an appropriate cleaning chemical (typically a dispersant) while the plant is in operation, a technique commonly used in the nuclear power sector. Investigations carried out since 2019 have shown that the technique could be successful in heat recovery steam generators (HRSGs).
Laboratory tests to evaluate an online cleaning technique
In 2022, laboratory tests were carried out in collaboration with the University of Liège to evaluate the performance of this kind of online cleaning technique. Tests were carried out on two types of tubes presenting significant oxide deposits, one from an all-iron unit and the other from a mixed-metallurgy unit. The tubes were subjected to conditions mimicking an HRSG installation and a dispersant was injected for four hours. Tests were conducted at different temperatures and pressures to learn which conditions would work best.
Promising results for all-iron tubes
The results are promising, at least for the all-iron tubes. Expert Anthony Senecat explains: “Within four hours, the cleaning dispersant successfully removed around 30 g/m2 of deposits in the all-iron tubes. The tests on the mixed-metallurgy tubes have been less convincing so far.”
Live tests are due to be carried out on an operational HRSG installation with all-iron tubes, with the results expected by the end of 2023.
Expert Jim Gripekoven points out that the tool has been built on solid scientific foundations: “The modelling is done in a state-of-the-art process modelling tool with a thermodynamic basis described in the literature. And it’s been validated through testing.”
The tool also anticipates upcoming EU regulations on renewable fuels of non-biological origin (RFNBO) with a view to meeting the 2030 targets.