Safe custom-built solutions for complex tasks
“If a human can’t do it, maybe a robot could?” Robots can indeed be crucial aids in the nuclear industry to carry out tasks where humans cannot because of danger from contamination or irradiation or other reasons. But the nuclear industry is unlike any other, and that means its robotized solutions must be too. ENGIE Laborelec designs, builds, qualifies, and implements all manner of robotized solution for nuclear power plants, meeting the highest nuclear standards.
Custom-built robots for high-precision work in radioactive environments
Laborelec specializes in applied robotics for the nuclear industry. Our robotics team produces solutions wherever a problem cannot be adequately addressed with an off-the-shelf product.
Very often these are for special one-off situations. Examples include non-destructive testing (NDT) or repairs inside the primary circuit of a nuclear power plant, or replacing primary components in a highly radioactive environment. These kinds of issues represent major challenges for robotic solutions because they demand ultimate precision and have to be controlled remotely following the highest standards.
Finding solutions that work in special contexts
The first step is a pre-feasibility study in collaboration with the power plant operator or with the OEM. Our multidisciplinary team of experts in nuclear operations, materials, NDT, and robotics analyses the problem to identify possible pathways, leading to conceptual solutions. We then work out in detail whether solutions are feasible, in close collaboration with manufacturing partners.
Developing designs and monitoring manufacture
If the study outcomes are positive and the proposed solutions and budget are accepted, we develop the design, including the detailed requirements, in line with nuclear industry standards.
Most often, solutions involve a robot machine and a series of technical modules for specialist processes such as various kinds of NDT inspections or grinding and cleaning operations.
We then closely monitor manufacture and carry out factory acceptance tests.
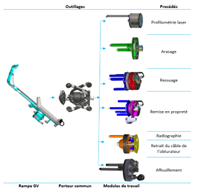
Qualifying solutions for use in the nuclear industry
We also develop the testing programmes and related procedures the solutions are required to pass if they are to qualify for use in a particular nuclear environment. Details of the testing programmes are submitted to the nuclear authorities.
To obtain qualification, comprehensive reports are compiled following tests carried out in full-scale test environments.
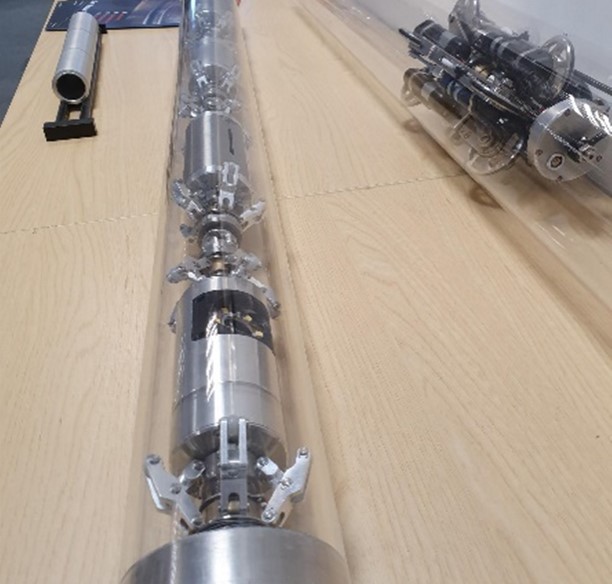
Preparing and executing on site
In some cases, Laborelec also works on site, always in close collaboration with the NPP operator, respecting nuclear safety and security requirements and standards. If the work is to be carried out by the NPP operator, we provide comprehensive training in the test environment.
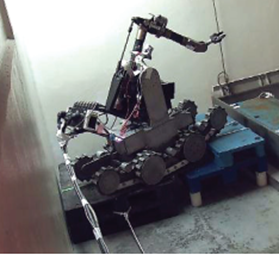
Solutions fit for the nuclear industry’s standards and practices
With decades of experience in the nuclear power industry and extensive expertise in NDT, materials technology, and robotics, Laborelec designs the right solution for every situation. Here are some recent robotized solutions we successfully created, qualified, and implemented.
A crawler to inspect, grind and clean primary circuit welds
Laborelec developed a custom-built robotic solution to carry out internal inspections in EDF’s nuclear fleet primary circuits. This included penetrant testing, radiography, visual inspection, and laser profilometry as well as grinding and cleaning elbow welds. The elbows had been replaced as part of LTO.
Specially designed to operate inside piping elbows, our robot crawler carries a range of modules, each for a specific part of the operation. The grinding module removes excess weld material, oxidation, and other superficial flaws, while the cleaning module uses solvents and suction to remove grinding dust and staining. The liquid penetration test module then sprays a dye into the pipework to detect surface discontinuity and look for the presence of flaws and cracks. A radiography module is used to detect potential weld defects, and a visual and laser-based profilometry module identifies imperfections in the metal, analysing weld profiles and material losses from grinding operations.
All the modules were rigorously tested and qualified to carry out work protocols in compliance with nuclear requirements. Staff were fully trained to operate the robot machinery.
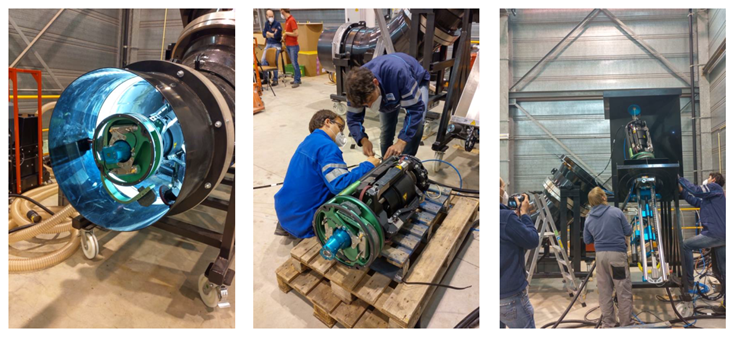
Inspecting radioactive waste vessels stored in inaccessible areas
For the Institut National des Radioéléments (IRE) in Fleurus, Belgium, Laborelec developed a solution for the inspection and lifetime assessment of six 40-year-old vessels containing radioactive material. Robotics was used because personnel are not allowed to enter the storage facility even for very short periods, given the environmental radiation levels above 250 mS/h.
In close collaboration with EQUANS, we developed a dual solution involving a robot crawler carrying out ultrasonic tests on the two more accessible vessels, and a drone-assisted visual inspection of the whole installation.
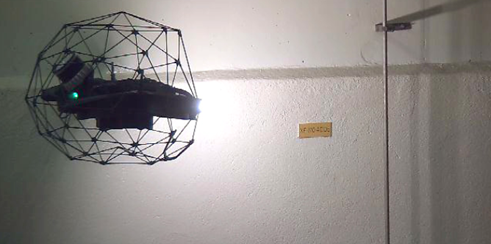
The facility’s complex topology meant that we had to mount cameras on the crawler and inside the space, allowing it to be operated via image-assisted remote control. The drone was equipped with lidar, a camera, a special antenna, and a protective cage so that it could be directed safely between the six vessels, recording images and taking scans of all the critical elements.
The dual solution was carefully prepared, developed, tested, validated, and carried out in the space of three months. A comprehensive report was produced, allowing IRE to put forward a strong case for the vessels’ lifetime extension.
Robotic inspection of venturi tubes
Laborelec was called in to inspect a number of venturi tubes which were thought to have become thinner due to erosion.
In collaboration with our robot manufacturer partner, we selected a laser profilometry inspection system with additional high-definition visual inspection. The system was adapted so that it could be inserted into the pipe through a valve, and moved across the venturi conversion and diversion sections, before we conducted factory acceptance tests.
We then constructed a mock-up of the actual pipe and venturi tube, including representative variations in thickness. This allowed us to test the system and develop a preliminary procedure for the live inspection, which was successfully carried out in 2021.
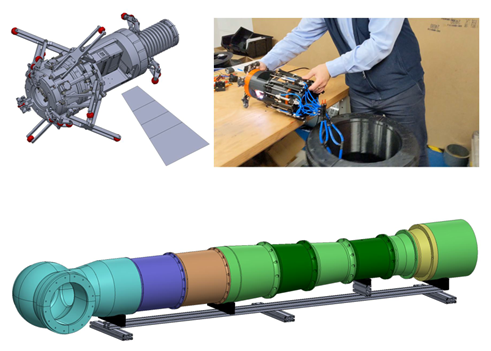