Nacelle-based LIDAR is the perfect way to accurately measure turbine Yaw performance
Every wind turbine operator is looking to maximize revenues from their wind turbines. Energy losses due to yaw misalignment can be significant, but effective correction will boost output. The LIDAR measures wind speed and direction between 80m and 400m upstream of the wind turbine, and determines how accurately the turbine is aligning itself to the incoming wind. With this information, the wind vane can be adjusted, and turbine settings can be modified to increase performance. Gains in annual energy production (AEP) can be as high as 5%.
ENGIE Laborelec owns and operates a fleet of nacelle-based LIDARs ready for deployment in static yaw correction campaigns.
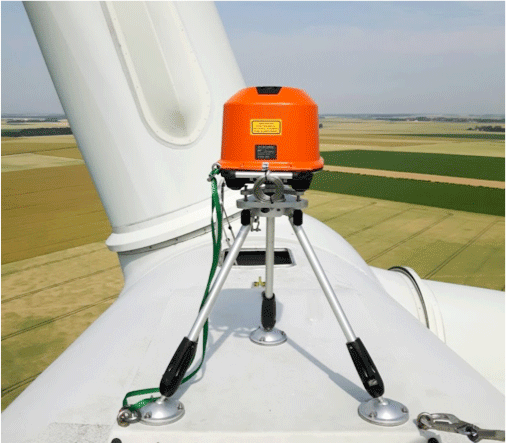
Measuring free wind for better accuracy
With LIDAR, wind speed and orientation are measured ahead of the turbine, by sensing so-called “free wind”. This is much more accurate than data from anemometers positioned to the rear of the nacelle, which measure the more turbulent air behind the blades.
Full ENGIE Laborelec service
ENGIE Laborelec takes care of everything during the measurement campaign:
Benefits of a nacelle-based LIDAR campaign
Clear reporting
Static and dynamic yaw performance are addressed in a brief report outlining the results of the LIDAR analysis. Static yaw misalignment can be corrected on all turbines models.
Misalignment and falling yield
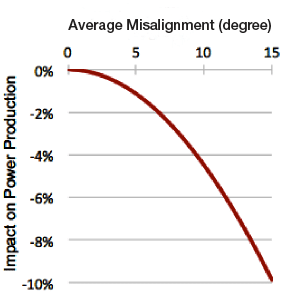
Output power decreases rapidly with the magnitude of the misalignment.
Installing a Lidar on a Nacelle:
Frequently asked questions
1. What does it take to install a nacelle-LIDAR?
Installing a lidar on a nacelle has become a routine task for ENGIE Laborelec personnel. For a variety of well-known OEMs, we know exactly where to install the lidar and how to attach it to the nacelle.
The lidar is firmly bolted to the nacelle roof using its dedicated tripod. During all installations on the nacelle, the crew respects a very strict working procedure in order to enhance the safety of all personnel. After the campaign, the drilling holes are repaired and the turbine is restored in its original state.
2. How long does it take?
Depending on the wind climate, a measurement period of 3 to 6 weeks is enough to measure the yaw performance, correct and validate the new settings.
3. What is the impact on AEP?
The impact on AEP depends on the severity of the misalignment. Even small misalignments of 3° are worth correcting for. Cases up to 15° misalignment have been found.
4. Can the LIDAR measure the Power curve?
Yes. The installation of a nacelle-based lidar allows to measure the free wind speed up to 400m upstream of the wind turbine. This enables an accurate measurement of the power curve. A lidar campaign for power curve measurement takes about 12 weeks.
5. Can it be used offshore?
Yes, the lidar is perfectly suitable for offshore applications.
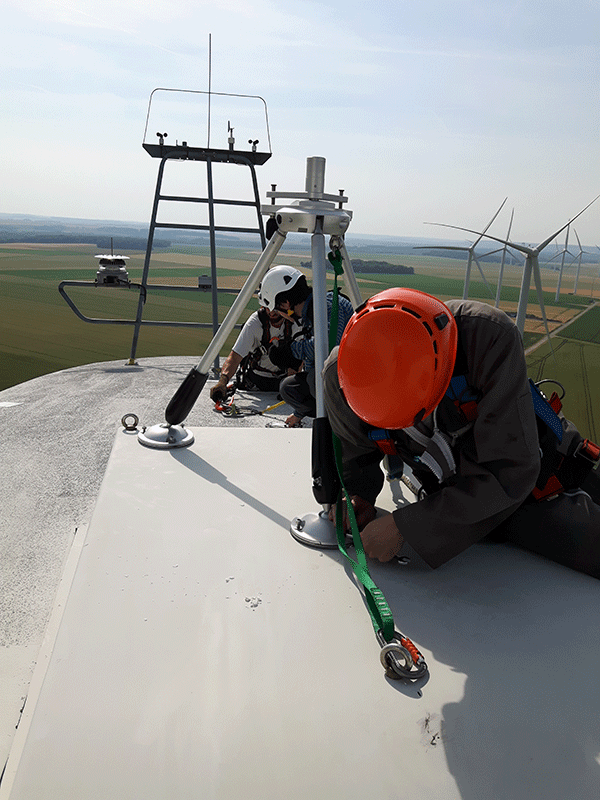
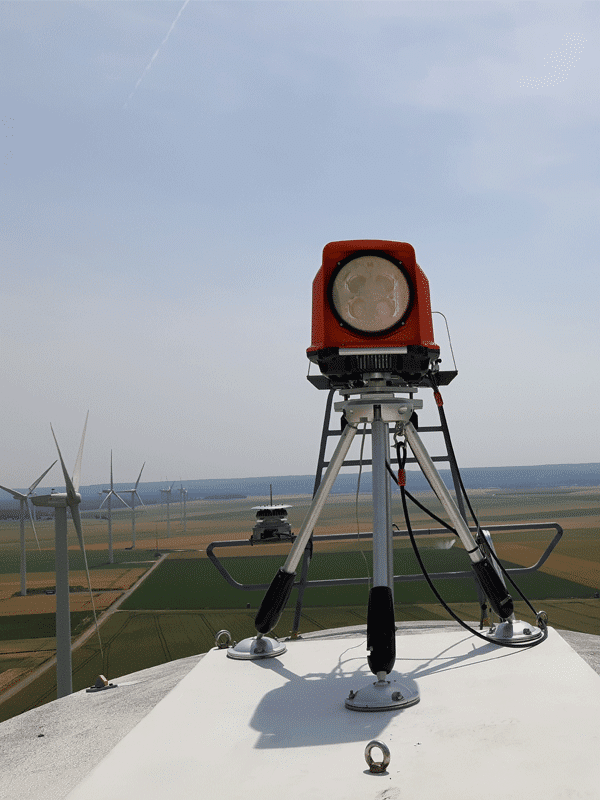
ENGIE Laborelec full service
As well as installing the LIDAR equipment, ENGIE Laborelec takes care of all the other aspects of the campaign, from the preparation of safety documentation to remote monitoring and data analysis.
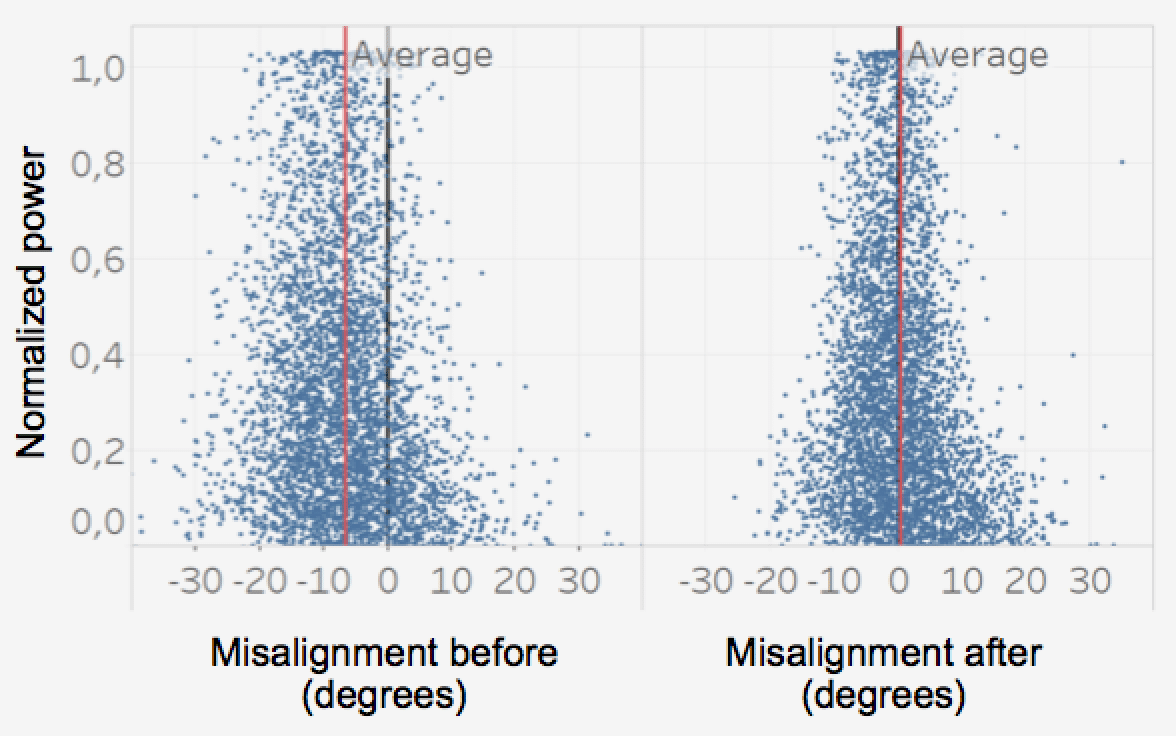
An effective re-alignment campaign
The LIDAR measures the precise magnitude of the static yaw misalignment. Then, after the corrections are carried out, the LIDAR confirms the effectiveness of the operation. The resulting increase in annual energy production can be as much as 5 %.